In this issue, we share with you the real case of vomiting toxin in wheat bread flour.
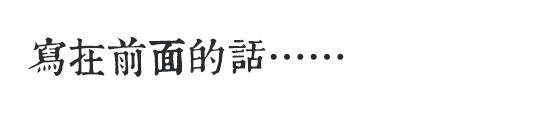
you know
The latest GB2762-2017 "Food Safety National Standard Foods for Fungalmycin Limits"
What is the maximum amount of vomiting toxin (deoxynivalenol) in wheat flour?
Not much to say, let's first share a set of cases:
First, the basic situation of sampling
On February 1, 2016, the General Administration commissioned a testing center to produce wheat bread flour produced by a food company limited by Shanghai E-Commerce Co., Ltd. (Specification: 350 g/bag, date of manufacture/batch number: January 7, 2016) Day) 6 bags.
After testing, the detection value of "deoxynivalenol" in this product is 1980μg/kg (standard index ≤1000μg/kg), according to GB2762-2011 "Food Safety National Standard Foods for Mycomycin Limits", it is judged as Batch of wheat bread flour is a substandard product.
Second, the verification process
On April 11, 2016, the Development and Separation Bureau of a city market supervision bureau received the unqualified inspection report of the wheat bread powder of the producer for a food company and the “Notice of the food safety supervision sampling unqualified sample verification and disposalâ€, immediately The inspection data was analyzed, relevant regulations were consulted, and a task force was established. On April 12, the Development and Separation Bureau of a city market supervision bureau delivered the inspection report and the Notice of Inspection Results to the Food Co., Ltd., informing them that they had the right to re-examine within 7 days, and issued an order to stop. The sales and recall notice required the company to immediately initiate a food safety second recall and report the recall plan and recall notice to the branch within 48 hours. On April 15th, the “Guide to the recall of wheat bread flour†was published on the website of the Food Authority of the province. After receiving the inspection report, the company initially determined that the batch of wheat bread powder failed to pass the sampling may be caused by the production of raw materials, so the right to re-examine was abandoned.
On April 21, the Development and Separation Bureau of the Municipal Market Supervision Administration, according to the inspection report, believed that the company was suspected of producing unqualified food, decided to investigate it, and delivered a suspension of production (sales) to the food company. Notice of bread flour and administrative interview notice; 988 bags of unqualified wheat bread flour (345.8 kg) recalled by the company, 3 barrels of additive baking enzyme (25 kg per barrel), 73 bags of raw flour (per The bag is 25 kg (a total of 1825 kg), and 350 kg of waste flour used in the washing machine at the time of production is sealed on site. On April 25, the legal representative of the company went to the Development Bureau of the Market Supervision Administration to accept the administrative interview.
After verification, the Food Co., Ltd. produced a total of 1,000 bags of bread flour, of which 2 bags were used for self-inspection in the factory and 998 bags were sold to its subsidiary in Shenzhen, the e-commerce company. Shenzhen Commodity E-Commerce Co., Ltd. sold a total of 10 bags in the No. 1 shop of the online shop, of which 6 bags were purchased by the State Administration for supervision and sampling, and the remaining 4 bags have been used by customers (1 bag in Shanghai, 1 bag in Shanxi, Jiangsu) 1 bag, 1 bag in Heilongjiang), all 988 bags in stock are recalled, the cost price is 3.10 yuan/bag, and the ex-factory price is 3.40 yuan/bag. The raw flour of the batch of bread flour processed by the Food Co., Ltd. was purchased from Guangzhou Industrial Co., Ltd., and the micro-added roasting enzyme was processed into a wheat bread flour for sale through magnetic separation, inspection and other processes. In order to find out the reason why the wheat flour powder deoxynivalenol exceeded the standard, on April 22 and May 12, law enforcement officers separately used the raw flour used to produce wheat bread flour to the provincial grain and oil product quality testing center. A sample inspection was conducted with a quality inspection station in another province. The provincial grain and oil product quality testing center inspection report showed that “deoxynivalenol was not detectedâ€; another provincial quality supervision and inspection station inspection report showed that “deoxynivalenol test results were 860μg/kg (standard index) ≤1000μg/kg)". On May 17, the law enforcement officers of the Development and Separation Bureau of the Municipal Market Supervision Bureau inquired by the experts of the National Food Quality and Safety Supervision and Inspection Center on the reasons for the excess of deoxynivalenol and the reasons for finding the cause. Experts believe that the reason for the excess of deoxynivalenol is that the possibility of raw material (flour) is large, but there is contingency. On May 18, law enforcement officers will legally seal 73 bags (25 kg/bag) of raw flour used for the production of wheat bread flour, 3 barrels of roasted enzymes (25 kg/barrel), and washing machine (test machine) with flour 350. Kilograms were unsealed.
On June 3, the Municipal Market Supervision Administration Development Branch issued an administrative penalty decision to a food company in the case, and made the following administrative penalties: 1. Confiscation of illegal income of 3.0 yuan; 2. Confiscation of illegal product wheat bread Powder 988 bags; 3, an administrative fine of 55,000 yuan. On June 7, 2016, the Food Co., Ltd. paid the fines.
Third, verify the problems and difficulties encountered in the process of disposal
In the process of verifying the handling of the unsatisfactory wheat bread flour in the production and operation of the food company, law enforcement officers encountered two major problems: First, although the company has no objection to the test results, it is difficult to sample differently or network samples. accept. Second, it was difficult to find the reasons for the unqualified products. Although the raw materials of the unqualified products were sampled and tested, and the relevant experts were consulted, but there are still doubts about the reasons for the existence of the unqualified products, and the lack of more scientific , rigorous, authoritative interpretation.
4. Measures taken during the verification and disposal process
In response to the problems encountered in the verification and disposal, after investigation and research, the Municipal Market Supervision Administration Development Branch has taken active and effective regulatory measures.
(1) Tracing the source and conducting supervision and sampling of food materials. In order to find out the reason for the excessive deoxynivalenol in the wheat bread flour, on April 22 and May 12, law enforcement officers sent the raw flour used to produce wheat bread flour to a grain and oil product. The quality inspection center and another provincial grain and oil product quality supervision and inspection station were inspected. The inspection report issued by the Provincial Grain and Oil Product Quality Testing Center showed that “deoxynivalenol was not detectedâ€. The inspection report issued by another provincial grain and oil product quality supervision and inspection station showed that “deoxynivalenol was 860 μg/kg (standard index ≤1000 μg/kg)â€, and the test results were not exceeded. Although the two raw materials are qualified for inspection, it can be seen from the test data that the possibility of contamination by deoxynivalenol is still present in the raw flour.
(2) Attach great importance to the problem of finding the problem in all directions. After discovering the unqualified products, the leaders of the Food and Drug Administration of the province attached great importance. On April 20, the responsible leaders and experts from the relevant departments led the food company to supervise the disposal and on-site inspection of the production situation. Patiently explained the importance and necessity of the food inspection department to carry out network sampling inspection, and consulted the experts, analyzed the reasons, and put forward specific guidance for the next disposal and control measures. On June 14th, the city sent high-precision wheat flour (testing materials) and recalled wheat bread flour to a provincial grain and oil product quality supervision and inspection station for testing. The high-precision wheat flour (testing material) inspection report showed “deoxygenated snow rot. Fusarium enol was 946 μg/kgâ€, and the recalled wheat bread flour test report showed “deoxynivalenol was 1350 μg/kgâ€. According to the repeated tests on raw flour and wheat bread flour, through consultation with relevant experts, it is believed that the reason why the batch of wheat bread flour "deoxynivalenol" exceeded the standard is the raw material (flour) problem, but there is contingency. Belongs to point pollution.
(3) Strictly control the barriers and require enterprises to carry out rectification from all aspects of production and processing. Although law enforcement officials initially determined that the reason for the non-conforming product is that the raw material flour is more likely to be contaminated, the control of the food production and processing links cannot be ignored. On the one hand, law enforcement personnel help enterprises to start from all aspects of production and processing, check items by item, strengthen rectification through improvement of process and environment, add color selection process in wheat cleaning process, increase color selection equipment, and use raw materials through optical principles. The mildew, discoloration and dissimilar grain granules were screened online, which reduced the content of imperfect granules and mildew granules in the raw materials. On the other hand, enterprises are required to strictly control the purchase of raw materials. When purchasing raw wheat grains, they strictly follow the requirements of national standards for water, imperfect grains and mildew granules, and require suppliers to provide the whole batch of flour. The test report must have the test data of the “deoxynivalenol†project; the enterprise also strengthens the sampling test when the finished product leaves the factory, and takes “deoxynivalenol†as a mandatory item, and conducts commissioned inspections on a regular basis. Ensure that the manufactured products are of good quality and safety.
(4) Strengthen supervision and implement the food production risk list into the enterprise system. In response to the food powder unqualified incident of the Food Co., Ltd., in order to strengthen food safety risk management and effectively prevent and resolve food safety risks, the Municipal Market Supervision Administration paid close attention to the standardization and standardization construction of food production enterprises, and formulated for the actual situation of enterprises. "Food Production Risk List", including: "Food Production and Management Ten Ban", "Food Production Risk Control Points and Preventive Measures", "Food Production Key Process Flows and Key Quality Control Points", "Food Supervision Bulletin", " Food Law Bulletin Board and other laws and regulations related to the food production of enterprises. In addition to requiring companies to publicize these laws and regulations in the production area, they also require that they must be the focus of corporate training. Through the implementation of the "Food Production Enterprise Risk List" into the enterprise and into the workshop, the regulatory requirements of "standardization, standardization, gridding, and traceability" have been further implemented, and the company's sound self-discipline, self-examination and self-correction mechanisms have been strengthened. The next step will be In more enterprises, the risk list will be gradually improved and finally achieved the goal of effectively preventing and controlling regional food safety risks.
V. Analysis and enlightenment
This case is a typical case of the food and drug safety department commissioned by the State Food and Drug Administration to conduct a food inspection in the country-level supervision and sampling, through the grassroots food supervision department to investigate and deal with the problem, to find the cause of the problem and ensure food safety. Through the verification and disposal of this case, it shows that in the daily supervision of food safety, the technical means has played an active role in supporting the technical support, and has become an effective means to check the hidden dangers of food safety and strengthen supervision.
(1) The implementation of sampling inspection is an important means of food safety supervision. The implementation of food sampling is not only a basic requirement for implementing the “four and two responsibilitiesâ€, but also an effective means of carrying out daily supervision. Today, with advanced technology and hidden risks, technical supervision has provided strong evidence for administrative law enforcers and played a deterrent role for offenders. Therefore, we should further increase the intensity of food sampling, expand the coverage of food sampling, organize the development of various types of food sampling, especially increase the network sampling, flight sampling, irregular sampling, close focus on key foods, weak links, etc. Frequently, deepen some regional, potential, and sensitive food safety issues, pay attention to the effectiveness of food sampling, and protect the health of the people.
(2) Strict sampling inspection specifications are the premise of food sampling inspection work. At present, with the wide application of the food sampling system, the standardization of the food sampling system needs to be accelerated. Since there is still a certain gap between the sampling inspection capacity of the grassroots supervisors and the requirements of the State Administration of Taxation, the intensity and breadth of the food sampling inspection training should be further increased, the “Food Inspection Manual†should be improved as soon as possible, and the sampling procedures should be strictly followed to refine the sampling requirements, especially The work flow of verification and disposal shall be in accordance with the actual situation. The system shall report to the actual law enforcement and provide advanced sampling equipment for the grassroots. At the same time, communication and coordination between departments, subordinates and regions should be strengthened, and food sampling inspections should be gradually implemented in accordance with the law, according to regulations and efficiently.
(3) In-depth investigation of the cause of the problem is an effective barrier to ensure food safety. The purpose of conducting food sampling is to find problems. The root of the problem is to dig deeper into the causes of the problems, eliminate potential risks, and solve problems with universality, specificity or specificity from the source. Both the regulatory authorities and food production enterprises should correctly face food safety issues, firmly establish a sense of urgency, problem awareness and responsibility, and leave no clues to explore the root causes of problems from multiple angles, all directions and long chains. At the same time, it is necessary to speed up the establishment of a food testing expert library to provide scientific, accurate and understandable food safety knowledge interpretation for regulatory authorities, enterprises and the masses.
(4) Strengthening food safety awareness is the fundamental guarantee for implementing the main responsibility of enterprises. The multi-format performance of food production and management and the unbalanced development of the central and western regions have brought pressure and challenges to food safety supervision. To this end, it is necessary to strengthen the publicity and education on food safety knowledge and knowledge of laws and regulations, especially the importance of food sampling work, so that enterprises from passive to active, from self-discipline to self-discipline, strengthen the implementation of the main responsibility of enterprises, and constantly create everyone Concerned about food safety and the social co-processing atmosphere for everyone to supervise food safety.
If the food processing enterprise has a fluorescence quantitative rapid detector, and the product quality is monitored in real time at the raw material end and during the production process, then the above “cups†can be avoided~
6. Fluorescence quantitative rapid detection system for vomiting toxin in Shanghai fly test wheat
Based on the world's leading fluorescence quantitative FPOCT technology platform, Shanghai Festo Biotechnology has developed a rapid quantitative detection system for vomiting toxins. This system combines the fast colloidal gold, enzyme-linked immunoassay and accurate chromatographic methods to quickly and accurately quantify within 8 min. The content of vomiting toxin in barley, wheat and flour is determined. The sample preparation is simple (only 7min), the operation is simple, only one step is needed, no standard is needed, no standard curve is needed, and the fluorescence immunoassay meter reading is used. The results are accurate and reliable, and can be printed on site. The accuracy is highly consistent with the detection results of HPLC method, which provides a new technical means for the rapid detection and control of vomiting toxins. It is suitable for all kinds of wheat storage, processing enterprises, testing institutions and Relevant government regulatory authorities.
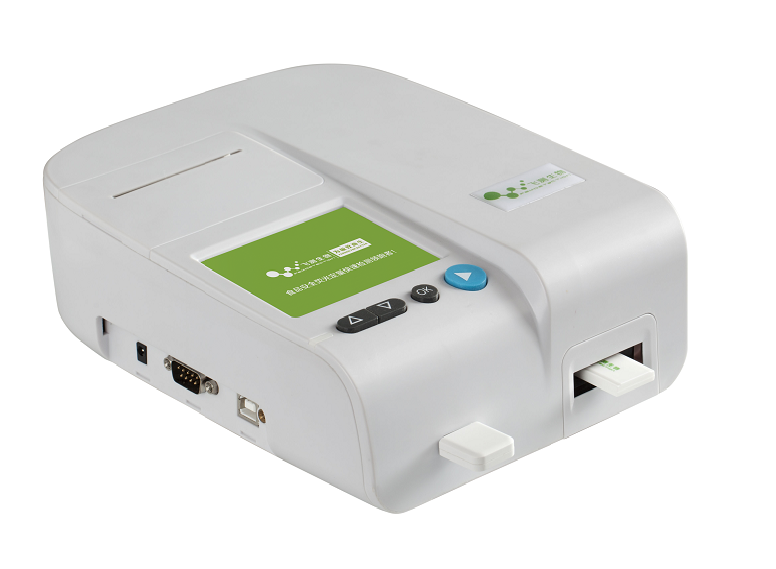
6.1. Vomiting toxin fluorescence quantitative test strip performance
ïµ Detection sensitivity: 25μg/kg;
ïµQuantitative linear range: 100μg/kg - 5000μg/kg;
ïµ sample pretreatment time: 7min;
ïµ Detection time: 8min;
ïµAccuracy: recovery rate is 80%-125%;
ïµ specificity: no cross-reactivity with other mycotoxins at a concentration level of 10000 μg/kg;
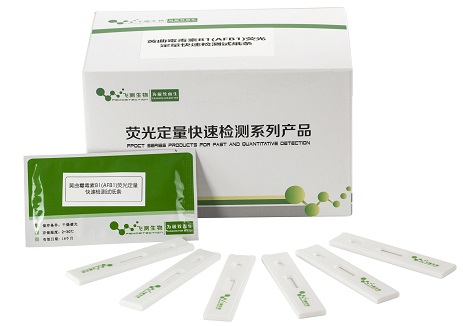
6.2. Sample preparation process
1, crushing;
2. Oscillation extraction (5min);
3. Centrifugation (2min);
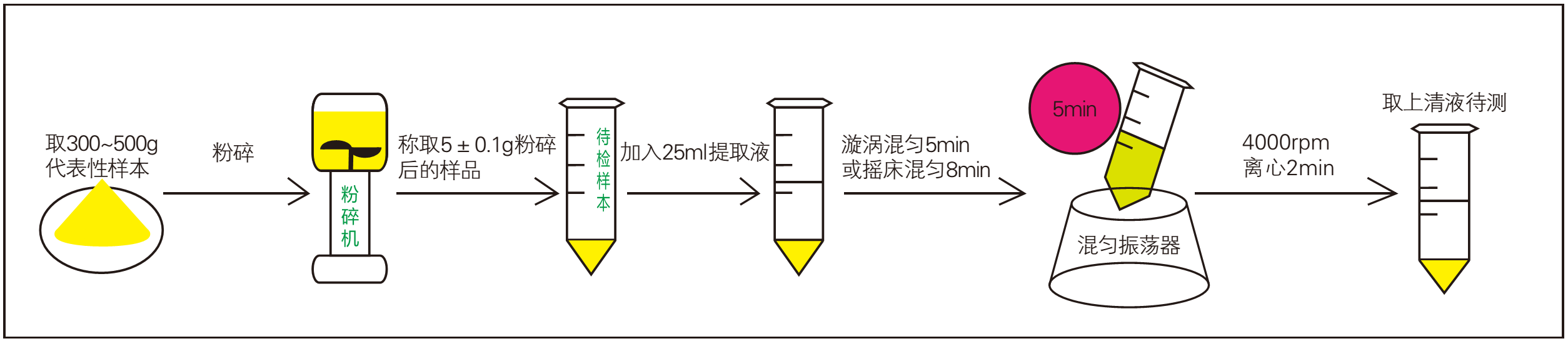
6.3. Detection operation process
1. Dilution;
2. Sample addition reaction (8 min);
3, reading, print test report;
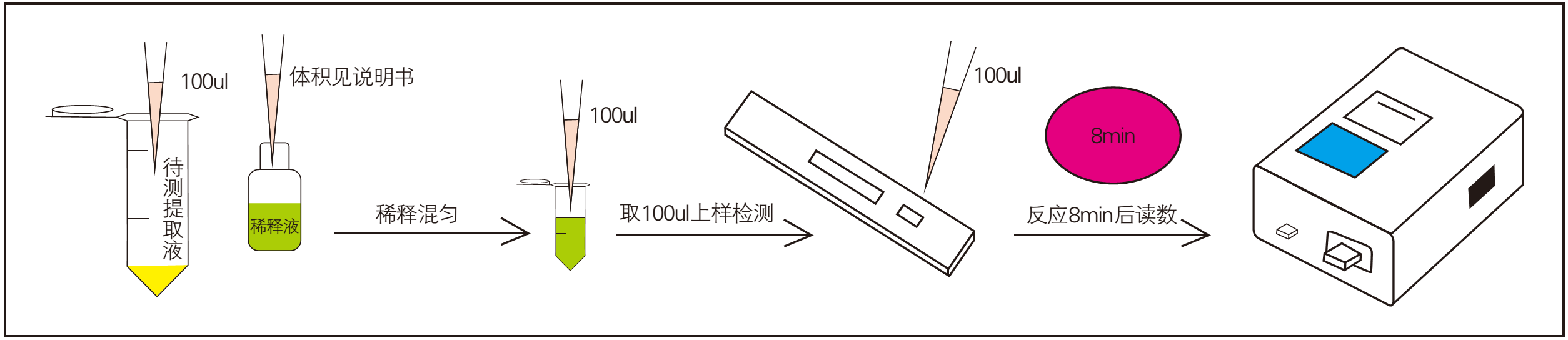
6.4. Results interpretation and output
The portable vomiting toxin fluorescence quantitative detector is used for reading, and the detection result is more accurate and objective, and avoids human error.
The test result will be presented on the liquid crystal display of the fluorescence reader. At the same time, the paper test report can be obtained by pressing the print button. In addition, after the WIFI data upload function of the instrument is turned on, the relevant data information will be automatically uploaded to the “Food Safety Traceability Managementâ€. Cloud platform for easy traceability and quality management.
6.5. Comparison of Shanghai Feifei Fluorescence Quantitative FPOCT Technology Platform and Other Methodological Techniques
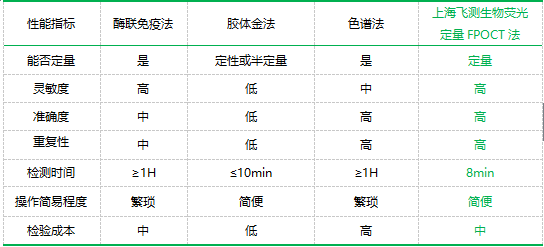
6.6. Advantages of Fluorescence Quantitative Rapid Detection Method for Shanghai Flight Test Vomiting Toxin
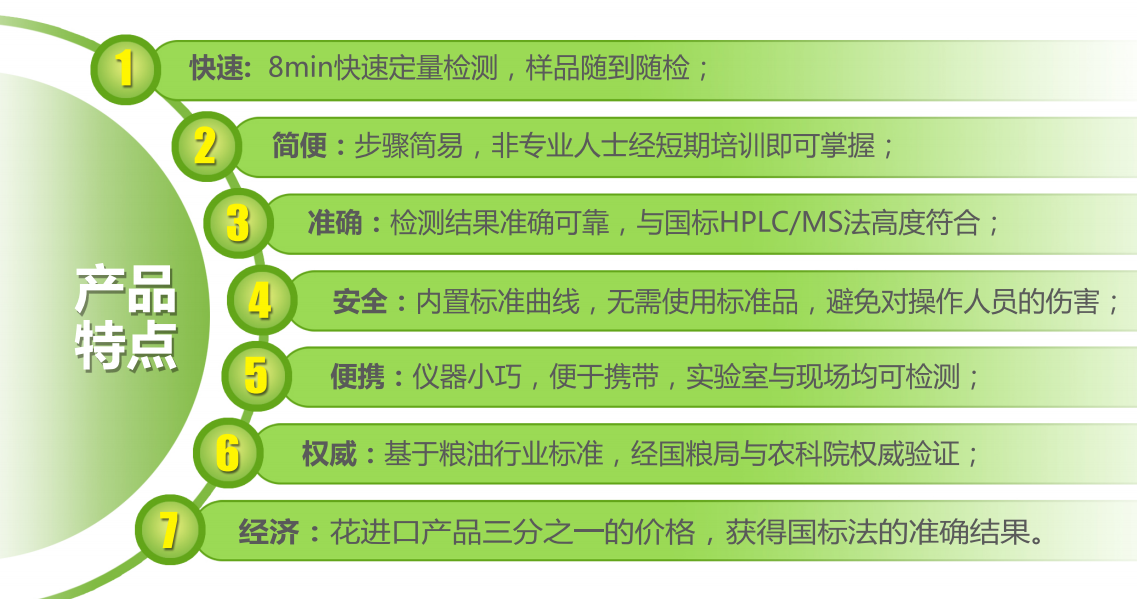
6.7. Basic parameters and performance of FD-100 vomiting toxin fluorescence quantitative detector
1. Instrument size: 210mm×197mm×84mm, touch screen size: 3.5 inches, weight: about 1kg, light and portable, compact, suitable for laboratory operation and on-site operation;
2. The excitation light source adopts LED, the excitation spectrum wavelength is λ0=365nm, the receiving spectrum wavelength is λ1=610nm; and the time-resolved fluorescence function has a reading time of 200us-600us, which improves the accuracy and specificity of detection;
3, measurement repeatability: precision CV ≤ 1.0%; inter-stage precision CV ≤ 1.5%; instrument signal-to-noise ratio: 0.01%
4, built-in standard curve, through the ID card to introduce the standard curve, no on-site calibration;
5. Scan the barcode through the built-in photoelectric scanner to switch different test items and batch numbers. The test items include aflatoxin, zearalenone, vomiting toxin, ochratoxin, fumonisin, T-2 toxin, etc.
6. The instrument detection response time is less than 8 seconds. The quantitative test results are displayed on the LCD screen. The displayed results include the project name, concentration, positive yin judgment, reference range, etc.
7, through the built-in thermal printer, can also be transmitted to the computer through RS232, USB interface, can also achieve remote data transmission through WIFI wireless module, to achieve traceability management of test data and information and big data analysis;
8, can store record detection time, sample number, product batch, detection value, negative positivity judgment and other information, data storage ≥ 10000;
9. Search according to date and test items;
Laryngeal Mask,laryngeal mask airway,pvc laryngeal mask,disposable silicone laryngeal mask
Anesthesia Medical Co., Ltd. , https://www.medicaldiverse.com