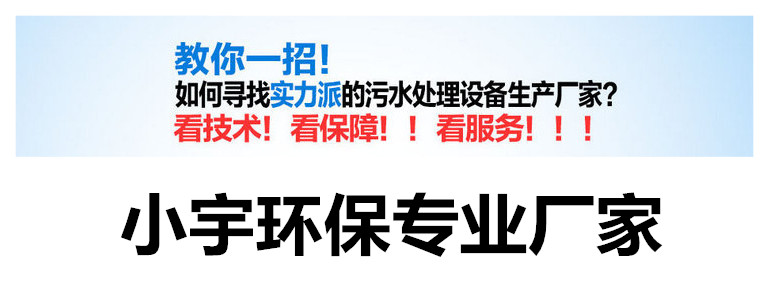
——Weifang Xiaoyu Environmental Protection Water Treatment Equipment Co., Ltd.
Looking for a FRP sewage treatment equipment installation, do you have the following problems?
? Is not a professional manufacturer? What is the price?
? Can free home installation?
What is the quality of the effluent? The floor space is not big?
Is the after-sales service good? Can you give free guidance?
Don't worry, Xiaoyu Environmental solves these problems for you! Weifang Xiaoyu Environmental Protection Co., Ltd. is a professional manufacturer of sewage treatment equipment. Our equipment is low in price and good in quality.
More than 30 installation masters across the country , as long as you purchase our equipment, we will send people to install free of charge.
You can rest assured that our equipment can meet the water standard, and the one-stop service before and after the sale will serve you!
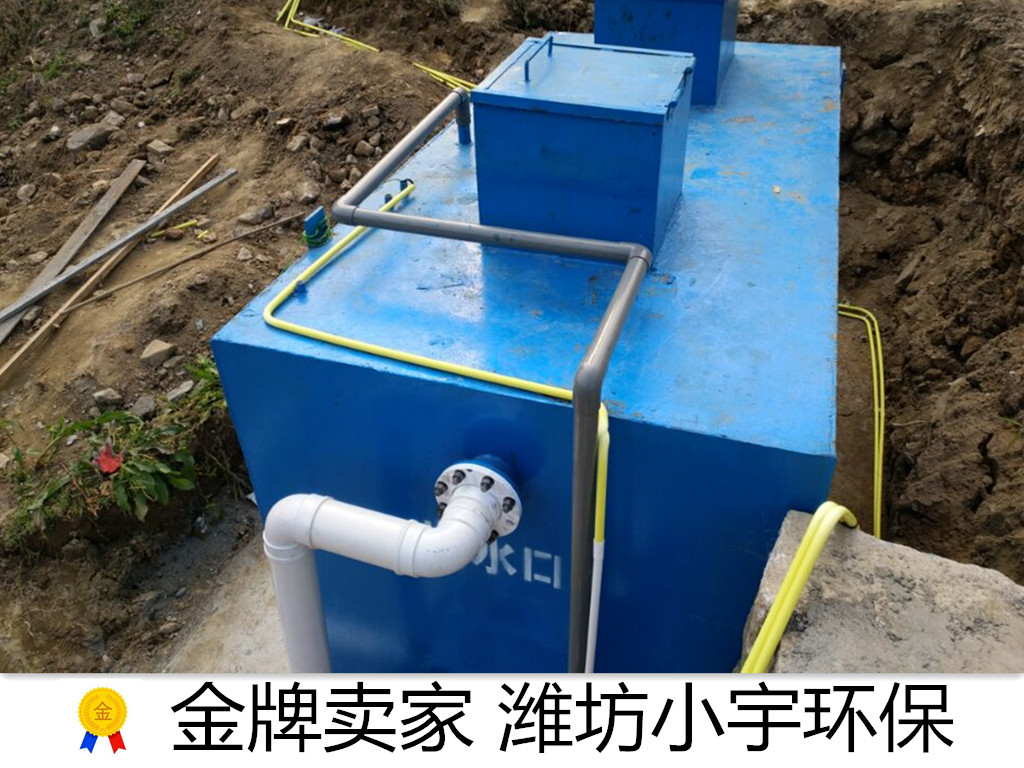
Equipment maintenance management
1 Equipment maintenance management content Establish mechanical equipment files, such as name, performance, drawings, documents, operation date, test data, maintenance records, etc. Adhere to the maintenance and repair system of mechanical equipment. Formulate maintenance procedures for mechanical equipment, such as technical standards for overhaul, procedures for overhaul, and acceptance of inspections. Establish a spare parts and spare parts system.
2 equipment wear and maintenance
A. Equipment wear concept The equipment will produce two kinds of wear during long-term use. One is material wear, which refers to the loss of friction and vibration caused by mechanical force during use; the second is technical wear, such as equipment being scrapped due to improper operation or other reasons, can no longer be used; or due to advances in science and technology, Equipment with the same performance and efficiency is constantly appearing,
As a result, the "value" of the original old equipment is reduced. Formally, the former is called physical wear and the latter is called invisible wear.
B. Equipment maintenance work category The maintenance and repair of equipment includes lubrication, anti-corrosion, cleaning, replacement of parts and components, etc. The equipment maintenance and repair are generally classified as follows.
(a) Daily maintenance This is an external maintenance such as cleaning, inspection, refueling, etc., which is undertaken by the operator and is one of the contents of the handover.
(b) The first-level maintenance inspection and maintenance of the vulnerable parts of the equipment, including cleaning, lubrication, partial and key disassembly and adjustment of the equipment, etc., are generally undertaken by the operator under the guidance of the full-time maintenance personnel.
(c) Secondary maintenance Strict inspection and repair of equipment, including replacement of parts and accuracy of repairing equipment. It is undertaken by a full-time maintenance technician.
(d) Minor repair This is a small local repair of the workload, only partial repair, replacement and adjustment.
(e) Medium repair This is a planned repair with a large workload. The sewage treatment plant is arranged once every 1-3 years, including the main part of the replacement and repair equipment, checking the entire equipment and adjusting the calibration so that the equipment can meet the requirements. Technical standards.
(f) Overhaul This is a planned repair of the workload, including the complete disassembly, inspection, repair, replacement, adjustment of the equipment, re-assembly into a new machine after the Zui, and repainting or painting the exterior of the equipment. It usually takes only a few years or even ten years to be completed by a professional (repair) factory.
C. The planned pre-repair equipment of the equipment will continue to “wear†the parts and key components during use, which will affect the performance, efficiency and safety of the equipment. The equipment top repair system is a work system that ensures that the equipment is always in good condition according to the "wear and tear" law of the equipment and through regular inspection and repair through routine maintenance.
The main contents of equipment pre-repair include routine maintenance, regular inspection and planned maintenance.
Operation and maintenance of grille decontamination machine
1 When installing the equipment, pay attention to adjust the clearance between the fixed parts and the moving parts (such as the guide rail and the sliding block) to ensure the smooth movement of the decontamination. Adjust the position of each travel switch and the collision block, determine the time interval of the time relay, etc., so that the equipment completes the complete cycle action according to the program specified by the design.
2 After the child is normal, the test run for several hours without load, and the water can be put into operation after no fault.
3 The refueling parts of the motor, reducer and bearing should be replaced with lubricating oil and grease as required. If ordinary wire rope is used, grease should be applied regularly.
4 Regularly check the operation of the motor, reducer, etc., and replace the worn parts in time. When the wire rope breaks beyond the specified allowable range, it should be replaced at any time. At the same time, the period of large and medium repair should be determined and maintained on time.
5 Frequently check whether the toggle bracket assembly is flexible, remove the foreign objects in the clamp, and check whether the screws of each component are loose.
Centrifugal blower operation and maintenance
1 When the blower is running, the blower should be checked regularly. Exhaust pressure and temperature, cooling water or oil level, pressure and temperature, air filter pressure difference. Do a good job of daily reading records and analyze and compare them.
2 Regularly clean the air filter to keep it working properly.
3 Pay attention to the influence of the intake air temperature on the operating conditions of the blower (centrifugal), such as the exhaust volume flow, the operating load and power, the possibility of surge, etc., and adjust the throttle device of the inlet guide vane or butterfly valve in time to overcome the intake air. The influence of temperature change on volume flow and operating load makes the blower safe and stable.
4 Always pay attention to and regularly listen to the sound of the unit operation and the vibration of the bearing. If abnormal noise or vibration is found, take measures immediately. If necessary, stop the vehicle to check the cause and eliminate the fault.
5 It is strictly forbidden to operate the centrifugal blower unit in the surge zone.
6 Check and maintain the motor or gear box according to the requirements of the manual.
7 One of the following conditions occurs during the operation of the blower, and should be stopped immediately to check:
A. The unit suddenly has a strong vibration or there is friction in the casing;
B. Smoke is emitted from any bearing;
C. The bearing temperature suddenly rises above the allowable value and cannot be reduced by various measures.
D. Oil should be changed 200h after the first driving. If the oil being replaced has not deteriorated, it can be reused after being filtered by the filter.
After the first driving, the oil sample was analyzed for 500 hours, and the oil sample was analyzed once a month. It was found that the oil should be changed immediately. The oil number must comply with the regulations and it is strictly forbidden to use other grades of oil.
E. Check the pumping position in the fuel tank. It should not be lower than the zoi low oil level line to see if the oil pressure maintains a normal value. Always check the oil temperature at the bearing outlet, which should not exceed 60 °C, and adjust the cooling water volume of the oil cooler according to the situation, so that the oil temperature before the inlet bearing is kept between 30 and 40 °C.
F. Clean the oil filter regularly. Always check the air filter for changes in resistance. Regularly clean and maintain to keep it working.
S. It is strictly forbidden to operate the unit in the surge zone.
H. Check the motor for apricot and maintenance according to the requirements of the motor manual.
The design principle of this sewage treatment project is
(1) Using advanced treatment technology and mature technology, the management process is simple, the treatment process is mature and reliable, and the long-term, stable and efficient operation of the sewage treatment plant is ensured.
(2) The treatment process and technology are economical and reasonable, saving investment and saving floor space.
(3) The odor pollution and noise pollution of the sewage treatment plant are effectively treated and meet the requirements.
(4) The treated sewage quality indicators all meet the emission requirements set by the buyer.
(5) Improve the level of pollutant reduction and comprehensive utilization of useful resources, and strive to obtain the social, environmental and economic benefits of Zui.
(6) Convenient operation and operation, simple maintenance and management, and low operating cost.
device installation
(1) Before installation, check each equipment out of the box and make a record.
(2) Examine the basics of civil works, including: geometric size, axis distance, elevation and appearance quality meet the design requirements, and make a record. The equipment foundation strength can reach 70% or more before installation.
(3) Find the basic vertical and horizontal center line of the equipment in place, and on the basis of the ink line, use the guide chain to fit the tripod or other force to hoist the equipment on the foundation, and make the center line and the basic center line complete. And looking for a leveling.
(4) The anchor bolts should be kept plumb in the holes, and there should be a certain gap between the surrounding and the holes. The bolts should be exposed to a certain distance. The nuts, washers and base should be evenly contacted.
(5) Installation of the equipment Except as detailed in the design drawings, refer to the installation instructions provided by the manufacturer.
(6) After the equipment arrives at the site, use the crane to hang it at the entrance and install it in place with a sling. Lift the open structure once.
(7) The installed equipment should be operated in a single machine. Before the test run, the motor should be tested for 2 hours separately. The parts should be lubricated and cleaned, and checked and repaired until the fault is eliminated.
(8) After the equipment is installed, it must have complete records:
1 Equipment unpacking inspection records;
2 Basic acceptance and release records;
3 Equipment installation leveling and correcting records;
4 Equipment commissioning record.
Self-control instrument
(1) Construction arrangements
The self-control professional construction schedule is generally interspersed in the process equipment installation, and the commissioning work is carried out with the unit and linkage debugging of the whole process pipeline equipment. This part is installed and debugged by a professional team.
(2) Construction points
1 The main control instrument mainly tests and controls the main parameters such as liquid level, pressure, PH value, dissolved oxygen, flow, and pipe opening and closing. The source is relatively scattered, and the piping at the source should be as close as possible to the transmitter and valve.
2 Cable laying should pay attention to the separation of strong and weak electricity.
3 Adjust the electric valve to stop electric when it is open and closed, and have the correct indication. The analog feedback valve position should be consistent with the site.
4 Note that the source point should be selected at a relatively stable water flow, that is, the straight line segment and part of the instrument should meet the requirements of the instrument manual.
Disposable Plastic Aprons,Plastic Aprons,Disposable Aprons,Disposable Polythene Aprons
Surgimed Medical Supplies Co.,Ltd , https://www.surgimedcn.com